The grinding processes
The new and economical Platform 3 enables a wide range of grinding processes such as; cylindrical and non-cylindrical applications of OD and ID, regular plunge and angular grinding, more complex operations such as profile, face, surface, and groove grinding, as well as the traditional JUNKER QUICKPOINT grinding process.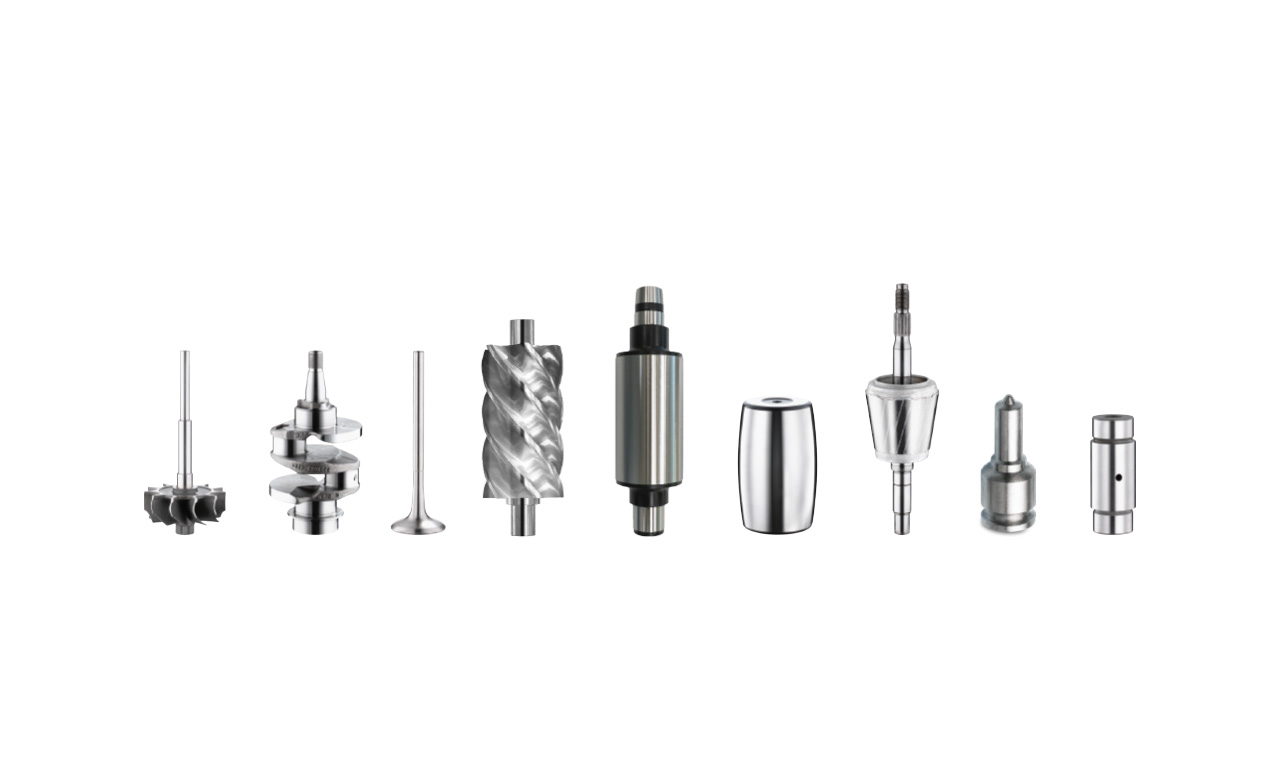
The machines
The design of Platform 3 allows a high degree of flexibility in machine configurations for specific projects. At the same time, it provides for individual customer requirements with a convincing price-performance ratio.
For different accuracy requirements in both main axes, X and Y, you can choose between different guide systems and drive variants. JUNKER offers the right solution depending on the to be ground requirements.
Another highlight of the new Platform 3 is the integrated automation concept. The machine can be loaded manually or fully automated. The internal gantry loading system can quickly adapt to new part configurations, with little effort and ensures smooth part handling. Easy access to all components on the outside and inside of the machine, combined with optimized setup capability, is the foundation of the entire system.